Hale uav composite wing structure design Written By leija Thursday April 28 2022 Add Comment Edit. The structural weight of HALE UAV is one of the most critical design requirements.
Hale Vtol Design And Development Blogs Diydrones
HALE Unmanned Aerial Vehicles UAV.
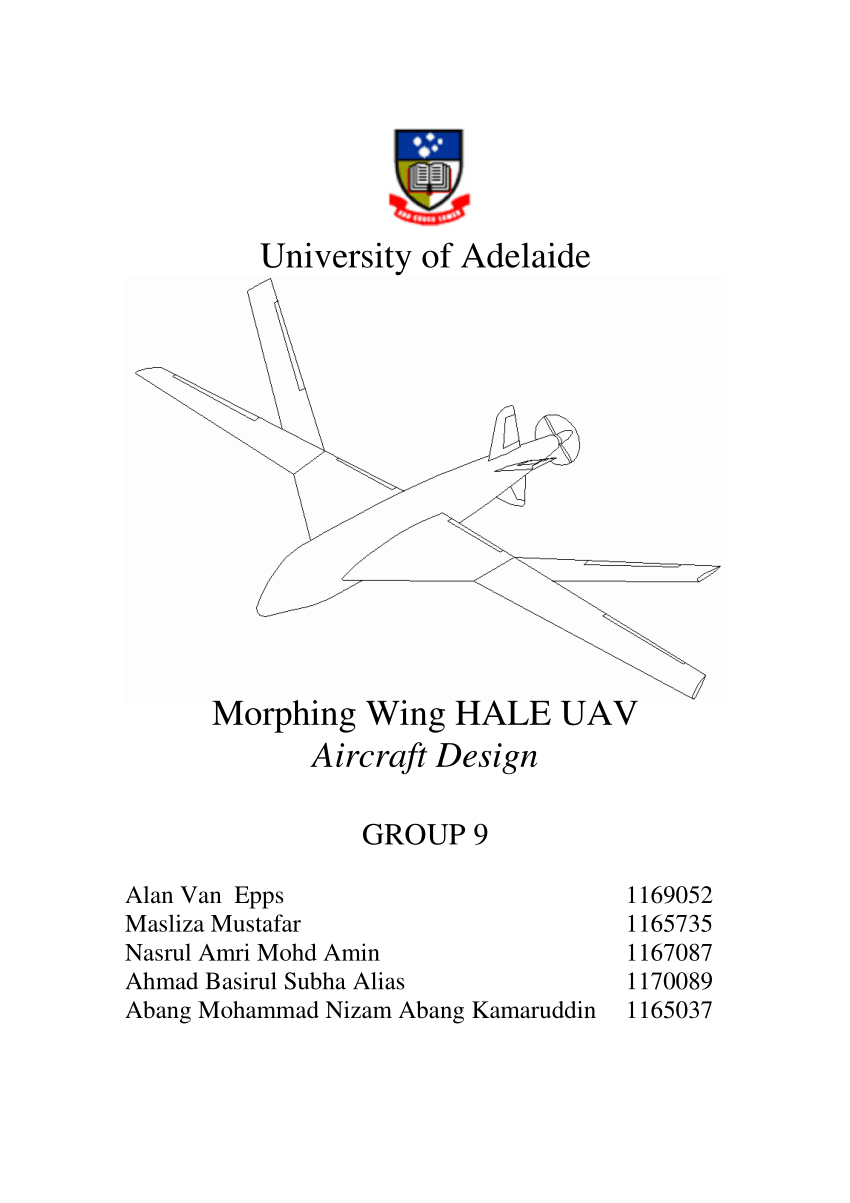
. Based on the results the wing composite structure of the maritime surveillance UAV is safe because it has factor of safety of 166 for load factor 38 and 335 for load factor -152 based on Tsai-Wu failure criterion. They achieved 253 of weight reduction. The wing is built modular with the length of each segment is 2 m.
Wing loading calculations were done based on the parameters. Designing the main wing and empennage of the EAV-. The constant chord wing part consists of two inner-wing tubular spar elements each 418 m long connect to a 42 m centre-wing-box.
High-altitude long endurance unmanned aerial vehicles HALE-UAV flying in the stratosphere can provide a useful platform for sensors to support a range of military and civilian surveillance tasks. The first paper deals only with the static strength analysis. Design of High Altitude Long Endurance UAV.
The structure of the UAV is also optimized by using composite materials in order to get a high strength-to-weight ratio analysis of the design structure configuration of. The scaled wing structure can be divided into a 112 m long constant chord inner-wing and two 657 m long tapered chord outer wings one for each side. The RQ-4 provides a broad overview and systematic surveillance using high-resolution synthetic aperture radar SAR and electro-opticalinfrared.
This site uses cookies. By continuing to use this site you agree to our use of cookies. A good way to meet this objective is to design an aircraft with a high aspect ratio wing enhanced lift-to-drag ratio and a lightweight composite airframe low wing loading2 This kind of aircraft is.
A wing structure consists of spars ribs reinforcements and skin and they were optimized considering two aspects of weight minimization and critical load maximization. Driven UAVs KARI has designed EAV-3 a solar-powered HALE UAV. UAV wing material characterization of the composites used in the UAV wing and prelimi-nary structural analysis of the UAV wing.
Finite element software ABAQUSCAE is used to predict the stress and deformation that occurred. For the 2nd generation HALE UAV ITB is designed having 16 m wing span with 04 m chord length. A model of the UAV was given and analyzed to design a wing box.
The concept of load bearing types of the skin are compared in the analysis. These prefabricated fibre composite components are joined using the same synthetic resin as a bonding agent. The structural design of the UAV composite wing regarding buckling analysis is more effective when the laminates are stacked up with high percent of - 45 degrees plies and the -.
Rigidity of a HALE aircraft wing structure. This is the second part on the design of a high aspect ratio HALE-UAV wing using composite materials. Conceptual design and construction of a UAV wing structure By SelmaRahman AnujanRanganathan.
In addition the structural stiffness for the high aspect ratio wing is another critical design requirement because the UAV has to keep the minimum clearance between wing tip and ground when the UAV is being towed. Indeed the low on-board power of the latter involve a high level of aero-dynamic and structural performance. A preliminary composite laminate structural design procedure is described which uses a NASTRAN-based Finite Element Analysis FEA and the Hierarchical Evolutionary Engineering Design System HEEDS MDO software to define a locus of acceptable optimized wing box design definitions.
Every wing segment will be joined using a glass-fiber joiner at the front spar. Manuscript received April 9 2016. For above design requirements the wing structure of the UAV has been.
Construction of a UAV wing structure SELMA RAHMAN ANUJAN RANGANATHAN KTH SKOLAN FÖR TEKNIKVETENSKAP. To find out more see our Privacy and Cookies policy. In addition the structural stiffness for the high aspect ratio wing is another critical design requirement because the UAV has to keep the minimum clearance between wing tip and ground when the UAV is being towed.
The spar also used a sandwich structure. The analysis is conducted with load factor of 38 and -152 which represent maximum and minimum load factor. The very flexible wing need to be designed so it can satisfy the deformation and strength criteria.
The wing was modeled as a beam structure. The internal structures have been designed to promote better flight and structural performances. This paper presents an analysis through simulation study of the structural design of a composite UAV wing.
The latest Lim et al 9 optimized wing design of Solar-HALE aircraft by considering interaction between aerodynamics and structures. This report presents the design of the wing structure for a UAV called Skywalker X8. The wing structure is modeled and analyzed using finite element to assess its integrity.
Structural Analysis of Composite Wing using Finite Element Method. HALE-UAVs are characterized by a high aspect ratio wing resulting in very flexible airframe. The real physical structure of aircraft.
The design variables are based on the positioning of spars and ribs of the structure. EAV-3 weighs 53kg the structure weight is 22kg and features a flexible wing of 195m in span with the aspect ratio of 174. The wing was made of a carbonepoxy laminate with orthotropic arrangement 0045-45 s.
This paper conducted a study on designing the 2nd generation of HALE UAV ITB which used composite materials in order to substitute balsa wood at some critical parts of the wings structure. The semi-monoque structure consists of one main mono-spar 4 major ribs carbon tubes and a flap. Optimization procedure to design composite wing box of solar powered HALE UAV.
2 Main wing structure The wing consists of an upper and lower shell of sandwith construction a number of ribs the main spar a nonbearing front wall a torque box and a number of chordwise stiffening strips Fig2. In this research the wing structure of initial version of HALE UAV is designed using carbon composite material. This paper is a continuation of the first paper and presents buckling and flutters analysis.
Subarus EJ207 engine was a 20-litre horizontally-opposed and turbocharged four-cylinder engine. The wing carries an elliptically distributed load along the span. The structural weight of HALE UAV is one of the most critical design requirements.
For above design requirements the wing structure of the UAV has been. Manufacturingisperformedatthe compositelaboratoryfounded in theDepartment ofAerospace Engineering and with hand lay-up and vacuum bagging method at room temperature the wing is produced.
Hale Vtol Design And Development Blogs Diydrones
Pdf Evaluation Of Novel Wing Design For Uav
Pdf Design Of A Swept Wing High Altitude Long Endurance Unmanned Air Vehicle Hale Uav Semantic Scholar
High Altitude Or Solar Powered Prototypes With Dlr Involvement Download Scientific Diagram
Structural And Aeroelastic Design Of A Joined Wing Uav Journal Of Aerospace Engineering Vol 27 No 1
Pdf Morphing Wing Hale Uav Aircraft Design University Of Adelaide
Pdf Design Optimization And Verification Of A Horizontal Stabilizer For The Seastryder600 Wing In Ground Effect Wig Aircraft Semantic Scholar
0 comments
Post a Comment